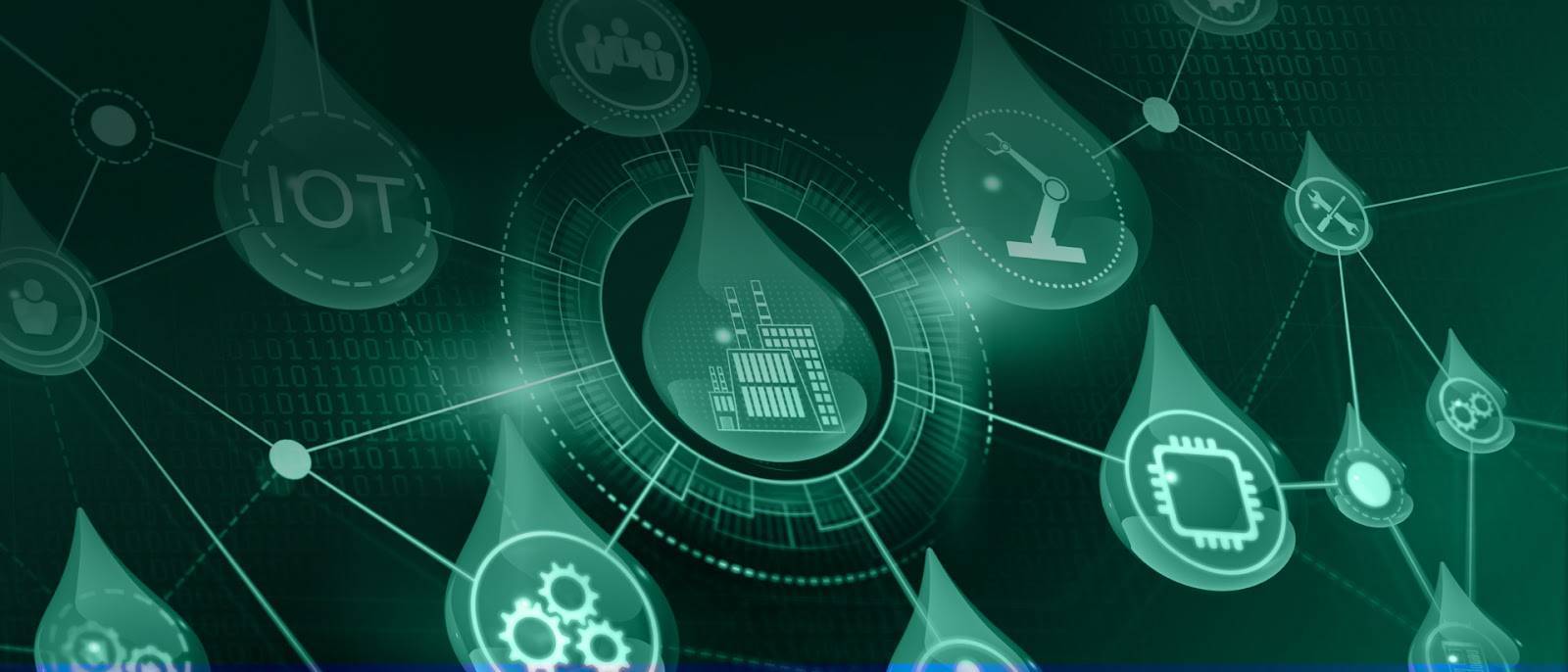
In recent years, the term “Industry 4.0” has been making waves across the global manufacturing landscape, ushering in an era of smart production and digital transformation. The industrial inkjet printing industry finds itself at an inflection point. The sector is poised for radical transformation by integrating technologies such as the Internet of Things (IoT), artificial intelligence, and robotics.
This article delves into the impact of Industry 4.0 on inkjet printing and explores opportunities.
It becomes apparent that adopting these technologies is necessary for advancing the industry. Industry 4.0 offers opportunities to improve quality, efficiency, and sustainability.
Industry 4.0 Unlocks Opportunities for Industrial Inkjet Technology
This new era offers opportunities to optimize printing processes, increase efficiency, and enhance product quality for the industrial inkjet printing industry. Just as the steam engine, assembly line, and computer revolutionized their respective epochs, Industry 4.0’s digital technologies are rapidly driving behind today’s most advanced inkjet printing innovations.
Across sectors, Industry 4.0 is transforming traditional business models, reshaping production lines, and redefining supply chain networks.
A prime example of this transformation is Siemens’ Amberg Electronics Plant in Germany. This facility manufactures Simatic Programmable Logic Controllers (PLCs), essential components for automation. Siemens has transformed this factory into a flagship model for Industry 4.0. By implementing IoT devices and real-time data analytics, the Amberg factory has seen impressive results:
- Increased Efficiency: The factory boasts an optimum product quality rate with interconnected systems and machines. The integrated systems provide immediate feedback if discrepancies are detected, allowing instant corrections.
- Enhanced Flexibility: The factory can produce over 1,200 different product types. By embracing Industry 4.0, Siemens can swiftly switch between product types, responding to market demands in real-time.
- Data-driven decision-making: Comprehensive data analytics offer insights into optimizing operations, reducing costs, and improving efficiency. The factory processes around 50 million pieces of data daily, driving continuous innovation.
Industry 4.0 has implications for many industry sectors.
In manufacturing, intelligent robots collaborate with human workers in smart factories, creating a new paradigm of human-machine interaction. In healthcare, interconnected devices enable real-time monitoring of patients, enhancing diagnostics and treatment. In logistics, autonomous vehicles and drones streamline the movement of goods, optimizing last-mile delivery.
The industrial inkjet printing sector is no exception.
The fusion of Industry 4.0 with inkjet technology has opened the door to an exciting era of digital innovation. As IoT-enabled printers connect to a network of devices, data flows seamlessly across the production line. AI algorithms process this data, enhancing the capabilities of inkjet printers and enabling them to operate in a digital ecosystem.
The convergence of Industry 4.0 and inkjet printing represents a significant shift from traditional, isolated printing processes to a fully integrated, digitized approach. This transformative journey promises to reshape the landscape of industrial inkjet printing, taking it to new heights as it navigates the uncharted territory of the digital realm.
Why Rapid Adoption Of Industry 4.0 Is Needed To Advance The Industrial Inkjet Printing Industry
Here are five reasons why the rapid adoption of Industry 4.0 is crucial for advancing the industrial inkjet printing industry:
- Improved Efficiency and Throughput: Industry 4.0 technologies can automate and optimize printing processes, leading to faster production rates. Companies can achieve higher throughputs, ultimately increasing their overall output and efficiency by reducing manual interventions and streamlining workflows.
See how Kao Collins prioritizes sustainability to benefit customers, employees, and communities.
Read More
- Enhanced Quality Control: Incorporating AI and machine learning allows for real-time monitoring and analysis of printing processes. By detecting anomalies and inconsistencies in real time, printing companies can quickly adjust parameters and maintain high-quality control standards, resulting in superior print quality.
- Reduced Waste, Increased Sustainability: Industry 4.0 facilitates the collection and analysis of vast amounts of data, which can be used to optimize printing processes and reduce waste. Companies can reduce production costs and environmental footprint by minimizing errors, reprints, and material usage.
- Maximized Resource Utilization: Integrating cutting-edge technologies with traditional printing methods enables companies to maximize resources and support sustainable production. Automation and data-driven insights help streamline production, ensure efficient resource allocation, and minimize outdated manual processes.
- Increased Flexibility and Adaptability: Industry 4.0 technologies provide real-time monitoring and control of printing systems, enabling quick adjustments and maintenance. This adaptability allows printing companies to respond swiftly to changing market demands and customer requirements, ensuring continuous operation and timely product delivery.
Case Studies: Embracing Industry 4.0 in Inkjet Technology
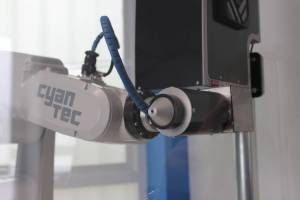
Cyan Tec robotic printing supports the growing 3D additive printing industry
1. Cyan Tec: Revolutionizing Robotic Inkjet Printing
Cyan Tec, a UK-based firm, represents the nexus between robotics and inkjet printing, showcasing how Industry 4.0 transforms the printing landscape.
Their groundbreaking robotic inkjet technology allows manufacturers to seamlessly incorporate direct-to-shape printing into production lines, addressing the printing of complex 3D products with robotic systems boasting up to six axes.
CyanTec’s solution promises efficient load/unload, mechanized product handling, and precision printing. Their emphasis on choosing a robotic inkjet solution resonates with the principles of Industry 4.0 and emphasizes the importance of expert integrators. Cyan Tec guides customers through printhead selections, inks and coatings, automation, and other considerations, positioning themselves at the forefront of industrial inkjet transformations.
2. MapleJet: Harnessing the Power of IoT for Advanced Inkjet Printing
Canada’s MapleJet exemplifies the potent benefits of integrating the Internet of Things (IoT) with industrial inkjet printing. Their product, the Hx Nitro industrial inkjet printer, leverages Industrial Internet of Things (IIoT) principles, prioritizing system integration, automation, machine-to-machine communication, and real-time data access.
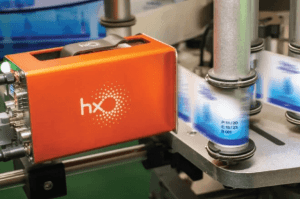
The Hx Nitro incorporates IIoT to prioritize system integration, automation, machine-to-machine communication, and real-time data access.
Such an approach ensures optimized production by minimizing human intervention and reducing the risk of production faults.
The company sees the importance of anywhere-anytime access with real-time data so companies can reduce production costs and their environmental footprint. This real-time monitoring can preemptively detect and address machinery issues, circumventing costly downtimes.
Moreover, when global challenges like pandemics necessitate social distancing, MapleJet’s emphasis on remote recovery, facilitated by IoT, allows engineers to access and fix machine issues remotely.
The forthcoming MapleJet Cloud feature aims to amplify these benefits, offering real-time notifications, alerts, and remote recovery capabilities, thereby solidifying its commitment to Industry 4.0 principles.
3. Heidelberg: Trailblazing Innovations
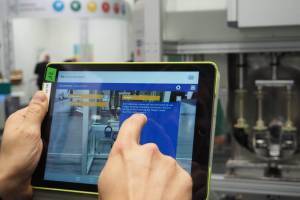
Heidelberg’s acquisition of DOCUFY supports the company’s digital strategy.
Heidelberg was founded nearly 200 years ago and has been at the forefront of printing. Today that includes embracing Industry 4.0 in the printing industry. The company’s “Heidelberg 4.0” initiatives integrate digital technologies and data analytics into printing equipment and processes.
While Heidelberg is more renowned for offset printing, they have ventured into digital printing, including inkjet technology. Their innovative adaptation and technological advancements show the potential of Industry 4.0 in industrial inkjet printing.
Heidelberg empowers its customers to make informed decisions through data analytics and visualization tools. Printers can access real-time production data and performance metrics to identify bottlenecks, make adjustments, and optimize their processes for better results.
Also, the company incorporates automation and robotics into its printing production, including automated material handling, setup processes, and autonomous job changeovers. These automation efforts lead to faster production cycles and reduced reliance on manual interventions.
Industry 4.0’s Current Impact on Industrial Inkjet Technology and an Eye on the Future
Industry 4.0, characterized by the convergence of digital technologies, automation, and data, significantly influences inkjet printing. While some aspects of this influence overlap, each plays a crucial role in reshaping the inkjet printing landscape.
Enhanced Precision and Quality through IoT-enabled Printers
IoT-enabled printers, equipped with sensors and data collection capabilities, offer enhanced precision in inkjet printing. These smart printers can adapt ink usage to the substrate, producing higher-quality prints. The use of better and adaptive ink also improves print quality.
The Future: Inkjet Technology Meets Creativity and Chemistry
IoT-enabled printers, equipped with sensors that capture data on multiple variables, could adapt inks for different substrates during production. By leveraging the power of sensor data and real-time adjustments, these printers showcase the potential for customization, precision, and efficiency in modern printing technology.
- Dynamic Chemistry: Developing smart inks with nanotechnologies could allow printers to adjust ink properties in real-time, tailoring the printing process to varying conditions and materials to meet unique quality specifications.
- Adjustments for Environmental Conditions: Humidity and temperature can significantly affect print quality. Integrated sensors could measure these conditions, and robotics could adjust ink parameters accordingly. For instance, the system might adjust drying times, ink flow rates, or viscosity in high humidity conditions to prevent smudging or bleeding. Conversely, the system could adjust the heating elements in colder conditions to ensure optimal ink adhesion.
- Production Monitoring: There’s potential for systems that continuously monitor the curing of LED or UV inks, optimizing the process in real-time. This ensures high print quality and reduces consumer risk. By adjusting line speeds, modulating light exposure, or other parameters based on feedback, the printing service providers can achieve optimal curing while also being alerted of any deviations from set standards.
Adaptive Printing Processes Using Real-Time Data Analysis
Real-time data analysis, combined with AI and machine learning, enables adaptive printing processes. By analyzing data from connected printers, companies can identify inefficiencies, reduce downtime, and optimize printing parameters.
The Future: Robotics in Inkjet Printing
The increased use of robotics in printing offers unparalleled precision and adaptability. Advanced robotics, equipped with sensors, accelerate printing and make real-time adjustments for consistent, top-quality prints.
- Print Head Adjustments: Intelligent robotic systems can adjust the position and alignment of print heads in real-time, ensuring the precise application of ink. These adjustments can account for minor discrepancies or shifts in the printing material, guaranteeing a consistently high-quality print.
- Material Feeding Systems: Advanced sensors can measure the feed rate of printing materials, enabling robotic systems to adjust material handling. For example, if a paper or substrate feed is detected to be misaligned or off-speed, the robotic system could correct it instantly, preventing potential printing errors or equipment damage.
- Optimal Speed for Quality: Using real-time data analysis, robotics can adjust the printing speed to maintain quality. For instance, the system might slow down when printing fine details, whereas broader and less detailed sections might be printed more rapidly.
This holistic integration of robotics and real-time data analysis can ensure that each printed item, whether a massive banner or a small label, is of the highest quality, regardless of external conditions or material variations.
Supply Chain Optimization via Interconnected Systems
Industry 4.0 technologies facilitate supply chain optimization through interconnected systems. This enables real-time tracking of orders and materials, allowing companies to create regionalized product packaging for one-off or short-run items such as wallpapers, fabrics, and clothing.
The Future: Innovative Inks and Intelligent Stock Management in the Supply Chain
In the pursuit of enhancing supply chain traceability, the development of innovative inks plays a pivotal role. By leveraging the chemistry potential, inks could be created to embed data directly into printed products, enabling easier scanning and tracking throughout the supply chain. For instance:
- Inks Chemistry with Embedded Technology: Integrating micro-transponders or nanotechnologies within inks could enhance product traceability and security. These smart inks could store the product’s information, manufacturing date, origin, and intended destination.
- Intelligent Ink Stock Management: As the inkjet printing industry evolves, so does the need for smarter stock management solutions. Advanced control systems can actively monitor ink stock levels, providing valuable insights like:
- Expiration Monitoring: Tracking ink expiration dates ensures that only fresh ink is used, maintains print quality, and prevents potential issues with faded or inconsistent prints.
- Ordering Advisories: The system could generate timely advisories or even automate re-ordering processes based on real-time data and purchase orders. This ensures that there’s always an adequate stock of ink, especially during peak demand periods.
- Ink Usage Forecasting: The system could forecast ink usage by analyzing past printing jobs and upcoming projects, assisting in better inventory management and reducing waste.
Combining innovative ink technologies with intelligent stock management systems will allow for an efficient, secure, and sustainable future in inkjet printing.
Supporting Environmental Challenges
IoT-enabled printers and data-driven ink usage can help reduce waste and water consumption. Improved ink formulations, supported by data analysis, can lead to more efficient and eco-friendly printing processes.
The Future: Smart Inkjet, Sustainable Results
-
- Advanced ink formulations could be developed to further reduce environmental impact. For instance, inks made from bio-based materials or those designed for easier recycling could contribute to sustainable inkjet printing.
- Industry 4.0 solutions could enable the tracking and reporting carbon emissions associated with the printing process. This information can be used to implement targeted reduction strategies.
- Industrial IoT could assist in monitoring and ensuring compliance with environmental regulations, preventing incidents that could result in fines or reputational damage.
Predictive Maintenance
IoT-enabled printers are revolutionizing the way we print and redefining equipment maintenance. These smart printers support predictive maintenance, providing comprehensive data on performance and wear. Analyzing this data allows companies to spot early signs of potential issues, ensuring the longevity of the equipment and minimizing downtime.
Common failure points that predictive maintenance systems can help identify.
- Leaks: Over time, ink supply systems may develop leaks due to wear and tear or faulty components such as O-rings. Predictive maintenance can monitor ink levels and flow rates to detect discrepancies, pointing to potential leak points before they exacerbate and compromise quality or equipment.
- Pump Failures: Pumps are vital for circulating and supplying ink to the printheads. Monitoring their performance can help spot ink flow or pressure inconsistencies, suggesting an impending pump malfunction.
- Clogged Printheads/Nozzles: Printheads and nozzles are susceptible to clogging, especially if the ink dries or there are contaminants in the system. Before a complete failure, clogged nozzles might show signs like inconsistent print patterns or reduced print quality. Predictive maintenance can detect these early signs by analyzing print outputs and nozzle performance metrics.
By identifying these common printer failures in their early stages, companies can carry out maintenance activities proactively, ensuring optimal printer performance and significantly reducing unplanned downtimes.
AI In The World of Industrial Inkjet Printing
Like other industries, Artificial Intelligence (AI) has the potential to reshape industrial inkjet printing. AI-driven algorithms analyze data from IoT-enabled printers to optimize print quality, reduce waste, and enhance efficiency.
Machine learning models assist in predictive maintenance, extending equipment lifespan and minimizing downtime. Furthermore, AI-powered adaptive printing processes adjust parameters in real-time, ensuring precision and adaptability. By enabling intelligent decision-making and automation, AI technologies could pave the way for smarter, more sustainable, cost-effective printing solutions.
Print Precision Redefined with Artificial Intelligence
Real-time data analysis, combined with AI and machine learning, makes adaptive printing possible. Companies like ImageXpert have offered high-speed cameras for drop analysis to generate information for optimizing printing. Equipment like this and other tools could support adjustments to nozzles, waveforms, material handling, etc. By analyzing data from connected printers, companies can identify inefficiencies, increase quality, and reduce downtime.
Such specialized solutions ensure printers operate efficiently while maintaining the highest print-quality standards. They analyze the output using advanced algorithms and machine vision systems, ensuring that each print meets the set criteria for clarity, color accuracy, and detail.
The Future: AI Diagnostics for Printing Excellence
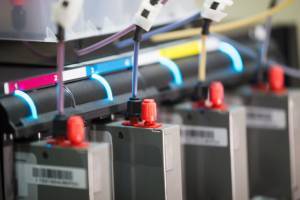
AI systems can diagnose ink flow problems as they develop.
The integration of diagnostic tools, propelled by AI capabilities, empowers printing experts to diagnose printer issues and make strategic optimizations.
- Combined with spectral analysis tools, cameras monitor real-time print quality, adjust printer settings, trigger alerts for operators, and more. When combined with AI, the results can be compared with information to optimize process improvements.
- Implementing automated inspection systems with AI and machine vision can enable the detection of defects or imperfections in real-time. These systems can trigger immediate interventions or alerts to operators, minimizing the production of faulty prints.
- Utilizing remote diagnostic tools with AI capabilities, technical experts can remotely assess printer issues, provide troubleshooting guidance to operators, and even make real-time adjustments to optimize print quality.
- Augmented reality tools, such as optimal printing settings, could overlay real-time information on a printer’s user interface. This assists operators in making immediate adjustments for better print outcomes.
Inkjet Printing in Industry 4.0: Revolutionizing Packaging, Textiles, and Ceramics
Packaging and Labeling Industry
Inkjet technology has revolutionized the packaging and labeling industry. IoT-equipped industrial inkjet printers are now standard in the sector and can monitor ink levels, print quality, and overall performance.
Packaging Inks
See Options
Furthermore, the advent of curable inks, especially UV inks, promises durability and resilience in printed labels and packaging. Such innovations have transformed the packaging landscape, offering consumers a blend of quality and aesthetic appeal.
Textile Printing
Industry 4.0 is weaving its way into the textile sector. The introduction of smart textile printers equipped with sensors ensures that parameters like fabric tension, color calibration, and ink usage are continuously monitored.
The Promise of Eco-Friendly Textile Inks
Read Now
The feedback allows instantaneous adjustments, promoting consistent print quality and minimizing waste.
Also, advanced systems facilitate efficient order placements, dynamically allocating print tasks to “micro-factories” based on their capacity and proximity to customers. This ensures faster delivery times and maximized production efficiency.
Ceramic Tile Printing
Tiles have been a canvas for artistic expression for millennia. With inkjet printing and Industry 4.0, the ceramic tile industry can produce intricate designs with unprecedented precision. Industrial inkjet printers in this industry are networked to collect vital data like ink viscosity, color consistency, and machine temperature.
Advanced AI algorithms then parse this data, fine-tuning the printing process to yield superior results.
Industry 4.0 Offers Disruptive Possibilities
Integrating Industry 4.0 technologies, including AI, IoT, and data analytics, propel the industrial inkjet printing industry into a new digital transformation era. As innovations converge, greater precision and productivity emerge to shape the future of industrial inkjet printing. Embracing these innovations will be essential for companies looking to stay ahead of the curve and seize new opportunities.